This article contains my technical opinions and is for general information purposes only. Product references are generic as different brands and products may have different features.
Introduction
In this document Texcan will endeavour to outline the Application Requirements, Standards and Certifications required to meet the cable needs for above ground or below grade installations. The types of conductors, insulations and jackets available for each power application.
Application Requirements
Flexible Cable Assemblies – The jacket, insulation and conductor need to be flexible to create a flexible cable. Typically, a high strand counts tinned copper conductor (1350 strands for a 535 kcmil cable) with EPR insulation and a CPE or XLPO jacket will provide the most flexible cable assembly.
Self-Extinguishing Cables – This is important if you are concerned with not spreading a fire within a facility through the electrical cables. The cable assemblies that are designed and built to meet certain requirements which provide self-extinguishing properties. An example of this is a medium-voltage cable that has an FT-4 or IEEE 1202 rating. The cables are placed in a vertical rack within a test chamber, they are then exposed to a 70,000 BTU/hr flame for a period of 20 minutes. Once the test is complete the burnt or charred section of the cables cannot exceed 1.5m / 4’11”. The balance of each cable beyond this point must be un-damaged.
Low Smoke Emitting Cables – This would be required If the cables are being installed in a closed environment like a below grade tunnel, station or gathering place containing people. In the case of a fire these cables will not emit enough smoke volume to prevent safe egress from a space or cause breathing difficulties. The CSA test requirement for these types of cables is to pass the ST1 smoke test.
Zero Halogen Cables – This is required if the cables are being installed in a closed environment like a below grade tunnel, station or gathering place containing people. When a cable assembly contains halogens and is exposed to high heat such as those found during a fire. The cable assembly will release halogens. When halogens are mixed with water (for example, the water used to fight a fire), hydrogen halides form hydrochloric acid, hydrofluoric acid or hydrobromic acid. These acids can damage or destroy critical structures, components and equipment, and increase toxicity.
UV Resistant Cable Jackets – UV resistance is advantageous when the cables may be exposed to direct sunlight. The UV will breakdown some jacket types of time. Cables that need protection form UV require a CSA SUN-RES rating.
2-Hour Fire Rated Cables – This is needed for critical circuits in a design. Where power of communication circuits must continue to function for a 2hour period after they have been exposed to the heat from a fire. Cables that meet this requirement must carry the UL standard 2196 certification.
Read our Transit Industry Flyer for our latest transit cable recommendations.
Standards and Certifications
The following is an overview of standards and certifications. If you require more detail our contact information can be found at the end of the article.
NFPA-130 – This document covers all aspects of electrified railway requirements with specific sections on cables to be used and a section on ventilation requirements. For the cables being used below grade they must meet:
1. A flame test of CSA FT-4 / IEEE 1202
2. Smoke density per UL 1685 / CSA ST1
FT-4 Flame Test – For a cable to pass the FT-4 / IEEE 1202 flame test, the cables must be placed in a vertical rack inside a burn chamber and subjected to 70,000 BTU flame for a period of 20 minutes. During this time the flame/ burn cannot travel up the cable assemble more that 1.5 meters or 5 feet.
ST1 Smoke Test – In a closed burn chamber the cables are mounted on a vertical rack. The cables are subjected to a 70,000 BTU flame for a period of 20 minutes. The emissions from the burn are collected and the amount of smoke particulate is recorded. It must be below 90m2 total volume and less that 0.25m2/s peak volume to pass the test.
Zero Halogen – As defined by most industry standards halogens can be present but must be below 0.5%.
Halogen Free – There can be no halogens produced during the manufacture or packaging of these cables. They are also required to pass a cable assembly burn test where no halogens are produced.
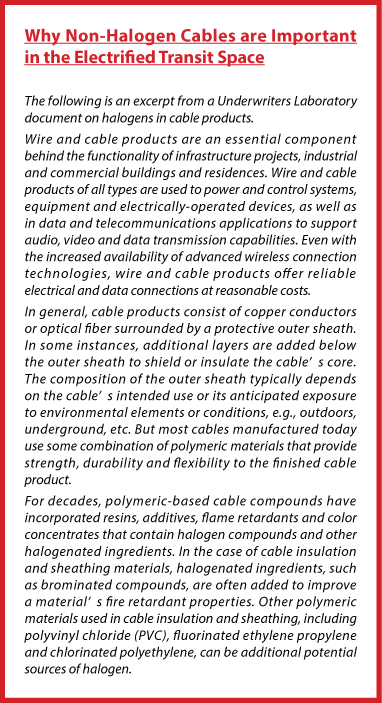
The Potential Harm From Halogenated Cable Materials
While cable insulation and sheathing materials incorporating halogenated ingredients may to be more flame retardant, they also emit a smoke when exposed to fire that can become toxic and corrosive under fire conditions. Specifically, halogens released from exposure to fire react with normally-occurring hydrogen to form hydrogen halide. When mixed with water (for example, the water used to fight a fire), hydrogen halides form hydrochloric acid, hydrofluoric acid or hydrobromic acid.
These acids can damage or destroy critical structures, components and equipment, and increase toxicity. Cables containing halogenated materials also produce significantly higher levels of carbon monoxide (CO) gas during combustion, further escalating their potential danger. Over the years, a number of high-profile fires have provided clear evidence of the potential dangers of cables shielded with materials containing halogenated ingredients.
To cite just one example, an electrical short-circuit in a Washington, D.C. Metro subway tunnel in 2015 resulted in the burning of legacy power cables that emitted noxious smoke and gases, leading to the death of one woman and sickening dozens of other passengers. The tragedy reportedly led Metro maintenance officials to speed up the long-planned replacement of older power cables with low-halogen content or halogen-free alternatives.
Conclusion
Thank you for taking the time to read our newsletter. At Texcan, we value your feedback and are here to address any questions or comments you may have. Don't miss out on our Transit Flyer and explore our Transportation webpage for products, project history, and more!
We are dedicated to supporting all your project needs, whether it’s cable specifications, capacity calculations, comprehensive planning, logistics, cable pulling calculations, or warehousing solutions. With extensive cable inventories across our Locations - Vancouver, Edmonton, Calgary, Saskatoon, and Winnipeg, we are well-equipped to meet your requirements.
We’re here to help! Contact Us for inquiries and quotes.
Dean brings over 26 years of wire and cable experience, starting as an Electrician before taking on roles in purchasing and project management. In 2006, Dean joined Southwire Canada, initially overseeing different business units, and later transitioning to the industrial group in 2010. By 2013, he became the Manager of Engineering and Product Support for the Canadian Division, with a specific focus on Electrified Rail and Electric Vehicles (EV). In 2022 Dean moved from Ontario to British Columbia and joined the Texcan Major Projects Group as a Transit Specialist. Dean’s Transit related major project experience: • Wilson Yard re-build • Edmonton Valley Line South • STM Subway MV and Traction cable retro fits • TTC Subway re-power • The Eglinton Crosstown LRT He can be reached by phone at 604-528-3667 or via email at Dean.Richards_ext@texcan.comAbout the Author