This article contains my technical opinions and is for general information purposes only. Product references are generic as different brands and products may have different features.
Introduction
Power cables, defined as cables rated 600V to 46kV for commercial and industrial applications, employ several shielding options. This discussion will look at shielding for power cables and will not get into other cables like data/electronic/audio cables, instrumentation cables, or utility cables, each of which have very different shielding requirements and constructions.
Purpose of Shielding
The main purpose of shielding Power cables is to increase the insulation’s life span by containing electrical forces within the conductor. The dielectric field created in energized cables results in electrical stresses when unshielded cables come in contact with ground (see Figures 1 and 2)*. The higher the voltage differential, the greater the resulting stresses on the conductor insulation.
In Canada, 5KV is a voltage level where shielding may be required. At 5KV the CSA cable standard, C22.2 #131 allows for either unshielded or shielded constructions, while CSA standard C68.10 requires all conductors to be shielded at 5kV and above.

Additional benefits of shielding include:
– Reduction of electrical noise induced on other cables in the vicinity.
– Grounding of touch hazards on both permanently installed power cables as well as temporary installations of mining cables.
– Compose part of a ground fault detection systems that monitor stray leakage currents.
There are 3 types of shields used in commercial / industrial power cables.
1. Copper tape shielding (most common)
2. Wire shielding (more commonly seen in Utility cables)
3. Copper braid shielding (commonly used in flexible cords and mining cables)
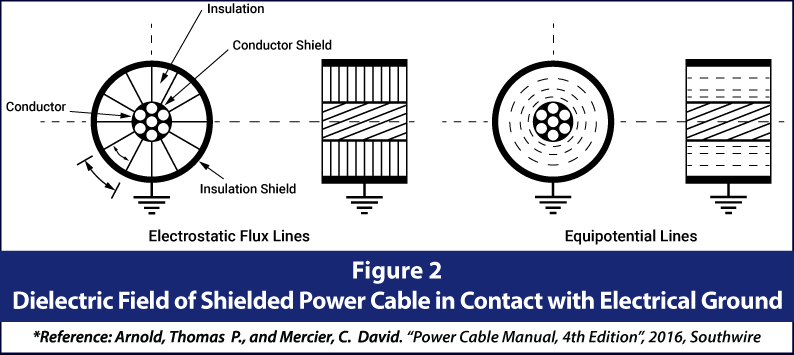
Copper Tape Shielding
Shielded power cables most commonly used in Canada for commercial and industrial applications are built to CSA C68.10. This standard allows for a wide range of copper tape types, thicknesses, overlapping, and tape application methods. As with all cables, anything is possible to have constructed, but due to the North American cable manufacturer’s limited CSA product approvals, manufacturing abilities, minimum order quantities and production lead times, in most cases specifiers are limited to the cable shield types found in constructions stocked by their local distributors.
Here is a summary of copper tape shield constructions that commonly may be found in Canadian distribution inventories.
1. Copper tape thickness – 3 mil and 5 mil (most common stocked construction)
2. Copper tape overlap – 15% gapped, 15% overlap, and 25% overlap (most commonly stocked construction)
3. Tape application – intercalated (two tapes), helically applied (one tape – most commonly stocked construction)
Some North American cable manufacturers offer customization of their CSA C68.10 power cable shield options, but most standardize on a single 5 mil thick copper tape, helically applied, with a 25% overlap. One might find other constructions in local distribution inventories, but in general 5 mil / 25% overlap is a standard product known for a generous amount of copper and overlap. Thinner tapes or gapped versions can allow for minor cost savings, but if the cable is installed outside or underground, it might be wise to use the full 5 mil / 25% overlap version to account for some corrosion of the copper tape over time.

Single Point vs Multi Point Bonding
Questions often arise regarding when to use multi point bonding over single point bonding. For shorter runs, single point bonding is commonly used. The benefit of this option is it eliminates circulating currents which require ampacity deration of the cables. The design concern is that at longer lengths, voltages may build up creating possible touch hazards. IEEE 575 limits this voltage to 25 Volts. See Figure 3* below for some calculated typical lengths to limit shield voltages to 25 Volts.
Conclusion
While there are many shield options that can be specified, practical considerations, like when you require the cables and the quantity required, frequently limit you to constructions stocked in local distribution. The CSA standards these cables are built to will all provide for shield constructions that will safely work, but you should consult with your local Texcan rep as to what is available and the pros and cons of those cable’s shield construction details.
About the Author
Blair Sackney has 23 years of wire & cable experience gained through major industrial, infrastructure, and commercial projects across North America. As an active IEEE member, Blair is passionate about sharing his expertise on better and safer cable installations.